Mörtel Rezeptur
Das Betonieren der Rumpfschale ist die kürzeste und wichtigste Bauphase, die über die Qualität des Rumpfes entscheidet, also über die Festigkeit und Oberflächenbeschaffenheit. Die maßgeblichen Faktoren sind Mörtel-Komponenten, Mischungsverhältnis, Einbringung (Auftragsweise), Verdichtung und später die Nachbehandlung bzw. Versiegelung.
Zement nach DIN EN 197-1
Die Entscheidung ob Zement mit hohem Sulfat-Widerstand hängt davon ab, wo der Rumpf seinen Einsatz finden soll. Soll der Standort in Flüssen oder Hafenbecken sein in wo Einleitungen stattfinden, ist ein Sulfat resistenter Zement sicher vorteilhaft. Beim Einsatz im Meerwasser ist SR Zement nicht erforderlich.
Zement-Sorten die üblicher Weise eingesetzt werden sind:
42,5 N 52,5 N 52,5 N – SR3 “Sulfat-resistent”
Einfluss der Lagerung
Zemente sind feuchtigkeitsempfindlich und sollten deshalb möglichst schnell verarbeitet werden. Da völliges Abschließen gegen Feuchtigkeit praktisch nicht möglich ist, sollten Zemente der Festigkeitsklasse 52,5 R höchstens einen Monat, Zemente der übrigen Festigkeitsklassen höchstens zwei Monate in trockenen Räumen gelagert werden. Bei Lagerung von Sack-Zement in trockenen Räumen ist mit einem Festigkeitsverlust zu rechnen:
- 10 bis 20 % nach 3 Monaten
- 20 bis 30 % nach 6 Monaten
Bei Mörtelmischungen
stellt sich die grundsätzliche Frage:
natürlicher Fluss-Sand (meist rund Korn oder scharfkantiger Struktur), oder gebrochener Quarzsand. (als Sackware aus dem Handel)
Sackware hat ohne Zweifel die besseren Vorteile.
- Genaue Sieblinien
- Reinheitsgrad
- Eigenfeuchte
- Lagerhaltung
- Dosierung beim Mischen
Doppelt-gebrochene Quarz Sande ergeben einen Putzmörtel mit zäherem Verhalten.
Rundkorn neigt mehr zur Entmischung und zum Fließverhalten des Mörtels.
Wenn man Schiffe in Entwicklungs- oder Drittländer wie wir bauen will, wird man meistens auf die vorhandenen Ressourcen angewiesen sein. Fluss-Sand mit scharfkantiger Struktur ist da die naheliegende Wahl.
In weniger technologisierten Ländern wird oft nur gewaschener Fluss-Sand als Rundkorn zu bekommen sein. Hier ist die Eigenfeuchtigkeit von wesentlicher Bedeutung. Jegliche Verunreinigung wie Blätter, Astreste, Katzenkot und Zigaretten-Kippen haben fatale Folgen.
Sand und Sieblinien
Für kleiner Schiffe mit mehreren Lagen von Armierungs-Gitter ist eine maximale Korngröße von 2 mm zu verwenden. Bei größeren Schiffen mit großmaschigen Streckmetall Matten oder Geogrit Basalt Matten Geflechten sind Korngrößen bis 5 mm möglich.
Die erste Wahl sollte doppelt gebrochener Quarzsand in Säcken sein. Dieser ist frei von Verunreinigungen und hat einen kontrollierten Feuchtigkeits-Wert. Gebrochener Quarz und scharfer Fluss-Sand ergeben ein zäheres Verhalten was den Auftrag begünstigt.
Eine möglichst dichte Packung des Korngerüsts (Appolonische Packung) bei Minimierung des Zementleimanspruchs und gleichzeitig guter Verarbeitbarkeit bzw. Verdichtungswilligkeit wird durch Sieblinien erreicht.
Eine Idealsieblinie ist die für näherungsweise kugelförmige Gesteinskörnungen nach Fuller. (Sieblinie 5mm Korn nach vorhandenem Gitter)
Befeuchtung
ist die Grundvoraussetzung für ein maximales Durchhärten. Sollte der Mörtel einmal abgetrocknet sein, stellt er die weitere Gefügebildung und Aushärtung ein. Ein erneutes Anfeuchten wird den Kristallisation-Prozess nicht wieder in Gang setzen. Die untere Kurve zeigt deutlich mit welchem Festigkeitsverlust dabei zu rechnen ist.
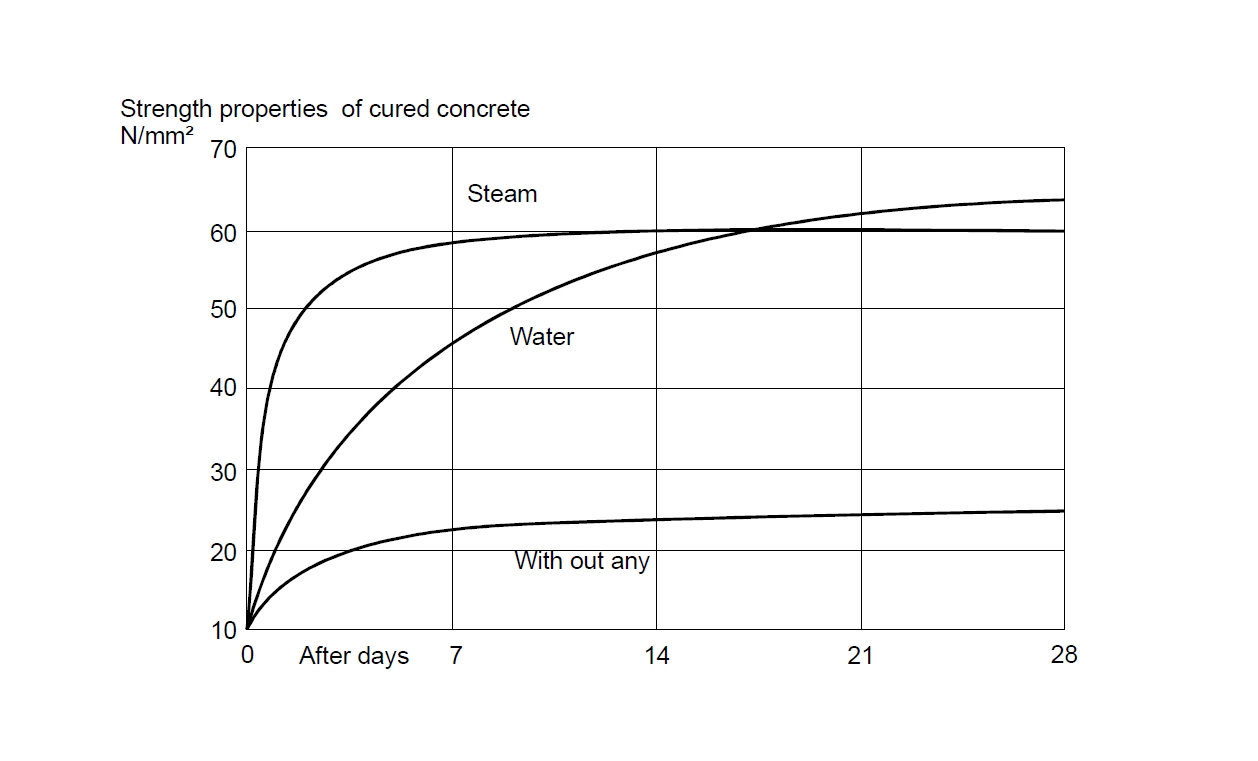
Wasser – Zement Wert
Dieser sollte konstant für den gesamten Rumpf sein und so niedrig wie möglich gehalten werden. Der Bereich von 3,5 bis max 4,5 ist gängig. Die Konsequenzen vom zu hohen W/Z Wert sind Wasserdurchlässigkeit und Verlust der Druckfestigkeit. Das Verdunsten des überflüssigen nicht im Zementleim gebundenen Wassers hinterlässt feine Kapillare die Zugänge für salzige Lösungen an die Armierung zulassen. Jeder überflüssige Liter Wasser schafft nach Austrocknung 1000 cm³ Kapillar-Poren
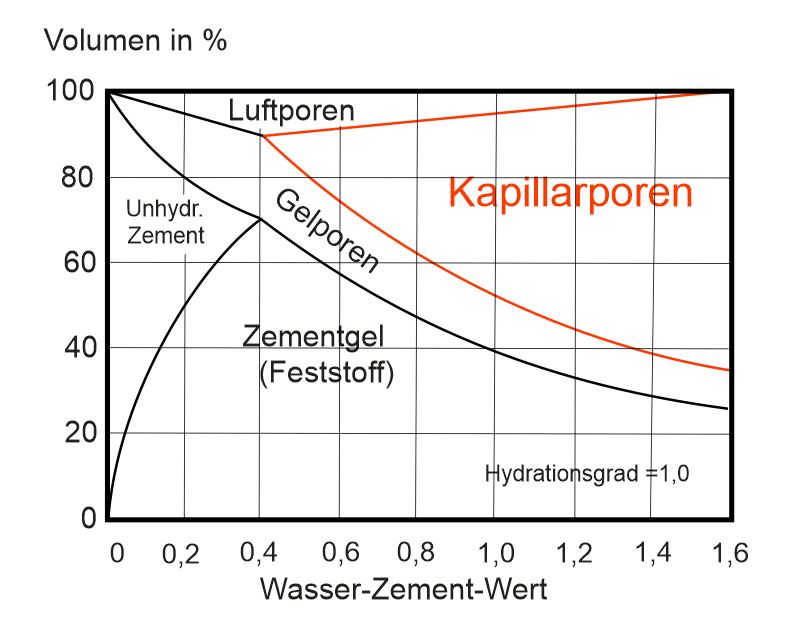
Verdunstungsverlust
in Relation zur Umwelt-Temperatur ist ein extrem kritischer Aspekt der die Festigkeit entscheidend beeinflusst. Besonders in tropischen Ländern bei besonders trockener Luft.
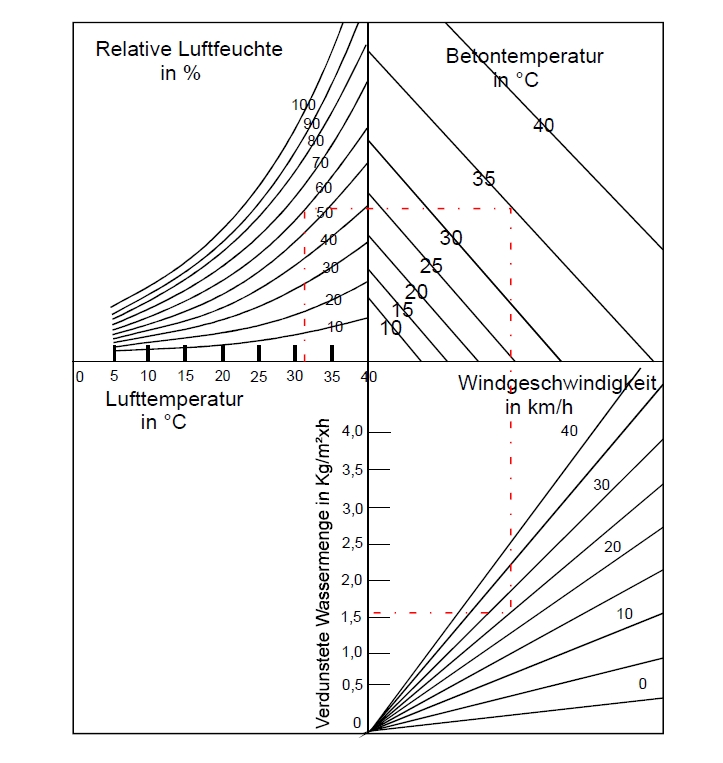
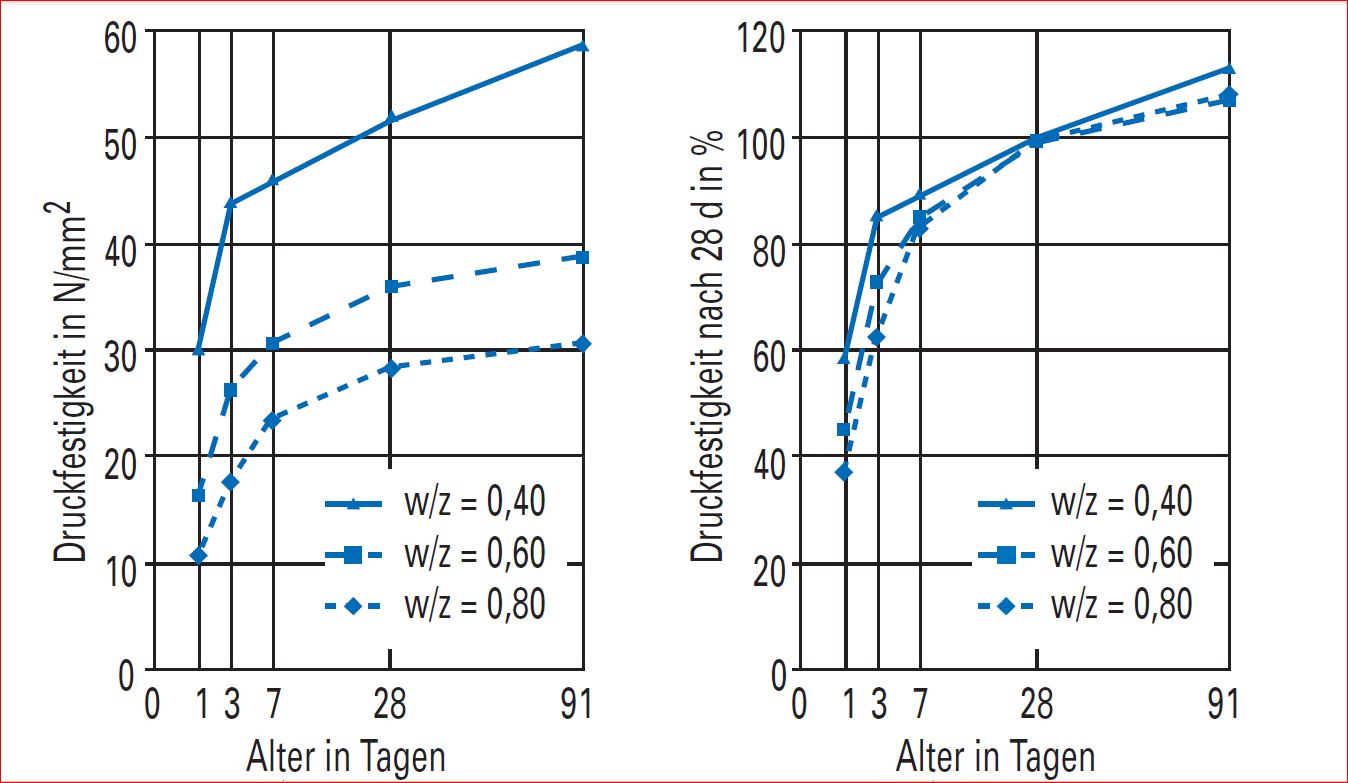
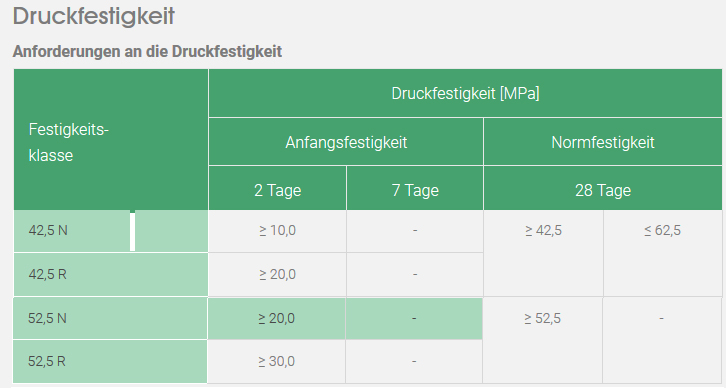
Fazit und Zusammenfassung:
Einen hochfesten Mörtel erhalten wir wenn der geringste W/Z Wert eingehalten wird, wir uns eine möglichst optimale Siebline annähern und der Mörtel für fast 3 Wochen gleichmäßig feucht gehalten wird.
Die Druckfestigkeit
fc von Beton wird in der Regel an gesondert hergestellten Probekörpern bestimmt. Üblich sind Würfel von 150 mm Kantenlänge (fc,cube) oder Zylinder mit 150 mm Durchmesser und 300 mm Höhe (fc,cyl), die nach in DIN 1048 genormtem Verfahren hergestellt und geprüft werden.
Zusatzmittel
Hier kommen im allgemeinen nur Verflüssiger und Erstarrungsverzögerer in Frage.
PCC Mörtel (Polymer Cement Concrete)